Cutting threads for a Bock 250 insert
When I made my first fountain pen, it was based on a kit. This involves drilling a hole in a piece of wood, and gluing in a brass tube. The brass tube is typically friction-fit onto a collar that’s threaded to receive the section assembly on one end, and the end cap on the other.
The next step was to turn a “closed end” pen, which didn’t rely so heavily on the brass tube – so the hole drilled in the wood could be of decreasing diameters to increase the strength and the design options, but still using the kit collar and section. A simple upgrade was to use a higher-end nib like a Bock instead of the cheap nib that came with the kit.
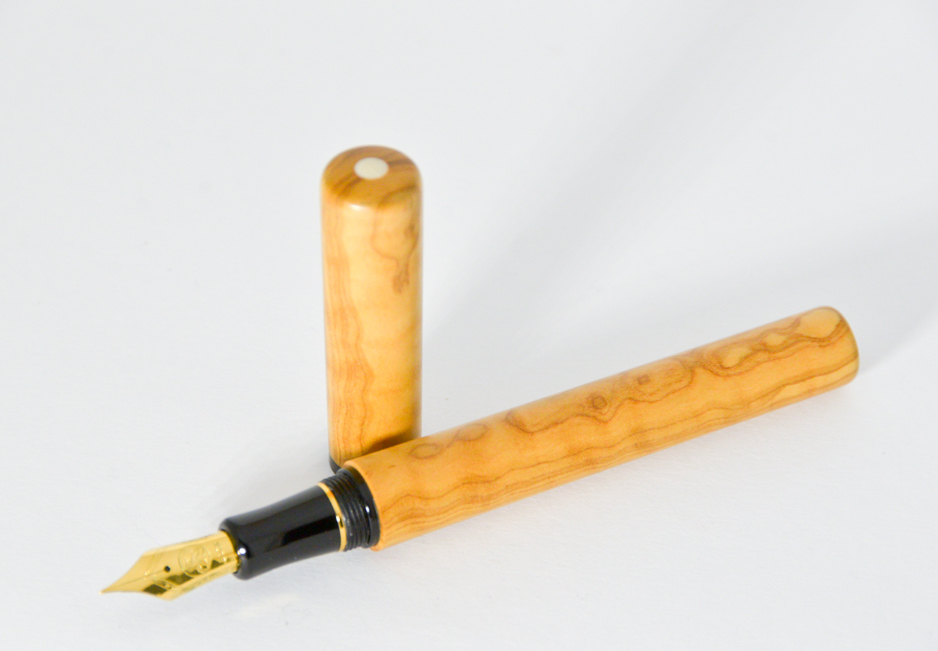
The next step was to replace the collar with my own, machined from brass, but still using the kit section, as shown below.
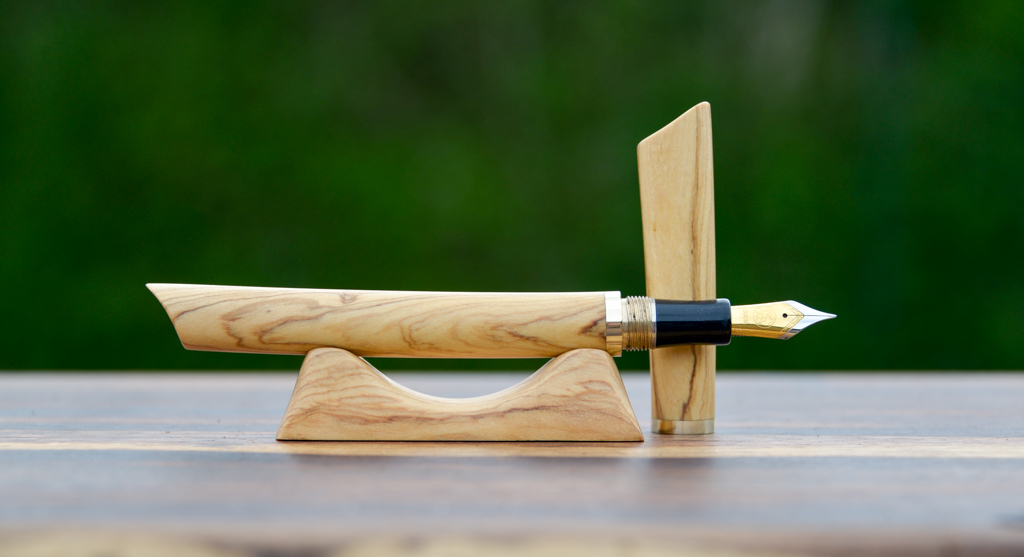
On to the next step! Time to make a section from scratch and use the Bock nib systems, which are comprised of a nib, feeder, and insert, which is screwed into the section with a fine thread.
So, I placed an order at Fountain Pen Nibs in Spain for a Bock 250 assembly, with some customisation applied to the nib (gold plating and engraving), and a new addition to my toolbox: a 7.9 x 0.6 mm tap for threading the section to receive the insert.
Saturday
Once everything had arrived, I spent the good part of a Saturday making a new section out of Ebonite, carefully drilling the right diameters from each end (making sure that the part to be threaded was reamed to a 7.3 mm diameter (7.9 – 0.6 = 7.3). Then came the time to put in the insert – and….
It didn’t work. Disappointment…
I tried reaming the now-threaded hole to 7.4 mm (just in case), but that didn’t help. The threads simply wouldn’t catch and pull the insert into the section.
Assumption #1 was that I bought the wrong tap. So, I double-checked my order, and that looked okay. Double-checked the tap and its case, and all appeared well…
Time to try something simpler, so I put a small plug of ebonite on the lathe, drilled and reamed it to 7.4 mm, and threaded it with the tap – going all the way through. The Bock 250 insert simply would not screw in – the threads would not grab at all.
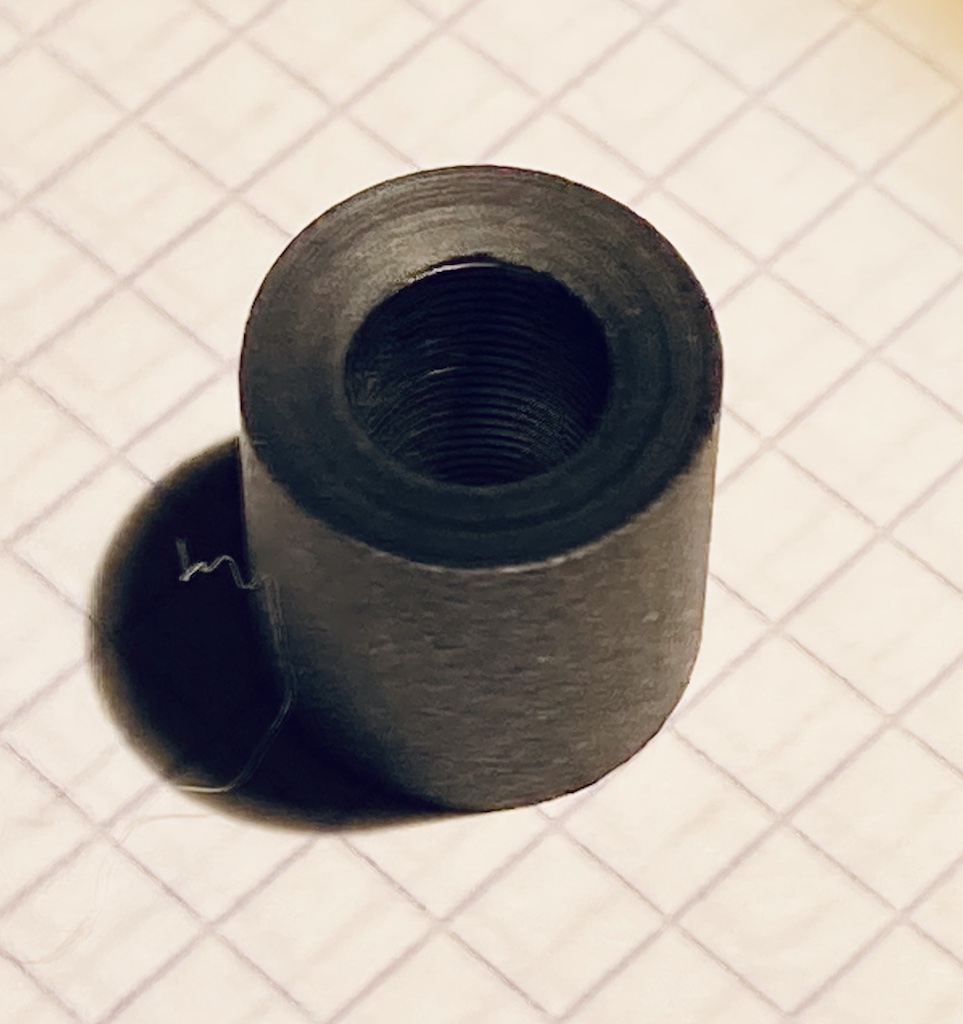
Neither would any of my Bock 250 inserts left over from previous projects, so it appears the problem MUST be the tap, right?
Sunday
Time to go back to the source – so I sent an email off to FPNibs to ask if they had any idea what could be the problem – however, by now it’s Sunday night, so rather than wait for an answer, I kept on digging.
That’s when I came across a posting on this page, where someone describes exactly the same problem, and feeling just a stupid as me… Misery loves company. One solution offered there was to ream the threaded hole out to 7.7 mm – but this leaves only 0.1 mm of thread to grab, and I’m not convinced that this is actually working (as I wrote on that forum thread). (One reason the threads are hard to see in that photo above is that I’ve reamed out the ebonite to 7.7 mm interior diameter… and it’s dark.)
More digging, and I found this page, where someone offered the solution of using the tap to make a custom die out of a soft metal such as aluminium to re-cut the threads on the Bock insert to match the threads made by the tap itself.
Monday
On Monday, I had access to a decent microscope, and, having a look in there, I could see that the threads on the Bock insert aren’t exactly what I would have expected. To use a very non-technical term, they’re quite chunky – almost like an Acme-type of thread, with a very flat, almost rounded top and bottom. This might explain the reason the insert isn’t grabbing on the tapped hole, since the tap tooth profile looks much sharper.
About 20 minutes later, I got an email from FPNibs saying that they had looked under a microscope and they found the same thing. Although they measure the correct diameter and thread pitch, the shape of the threads themselves look just a little fat…
I wrote back that I’d try the make-your-own-die trick when I got home from work.
That afternoon, I put a scrap piece of brass on the lathe, and then did the following in the following order:
- drilled a 7.0 mm hole
- reamed it out to 7.4 mm
- reamed a very gentle taper at the entrance of the hole
- threaded the hole with the 7.9 x 0.6 tap
- cut some small chip-clearing grooves with a small file that’s flat on one side and rounded on the other, keeping the flat side as the cutting edge
- cleaned up the resulting burrs with the tap
In the end, the result looks like this:
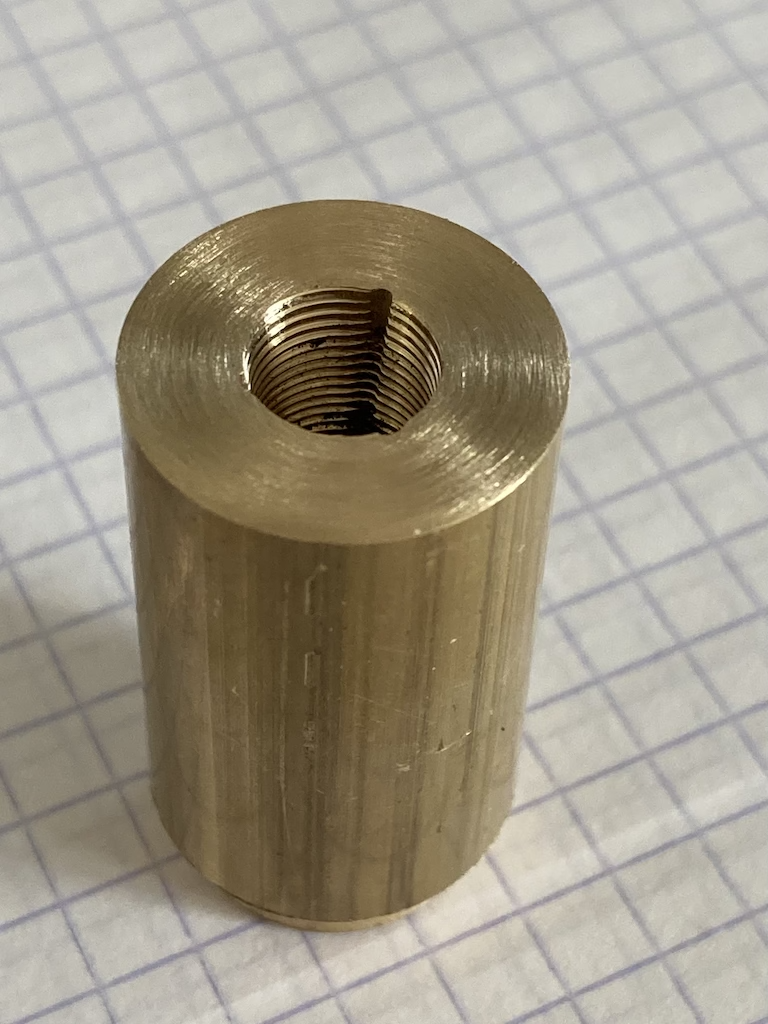
It might not be pretty – but it does the trick! I used it to re-cut the threads on a Bock 250 insert and the result looks like this:
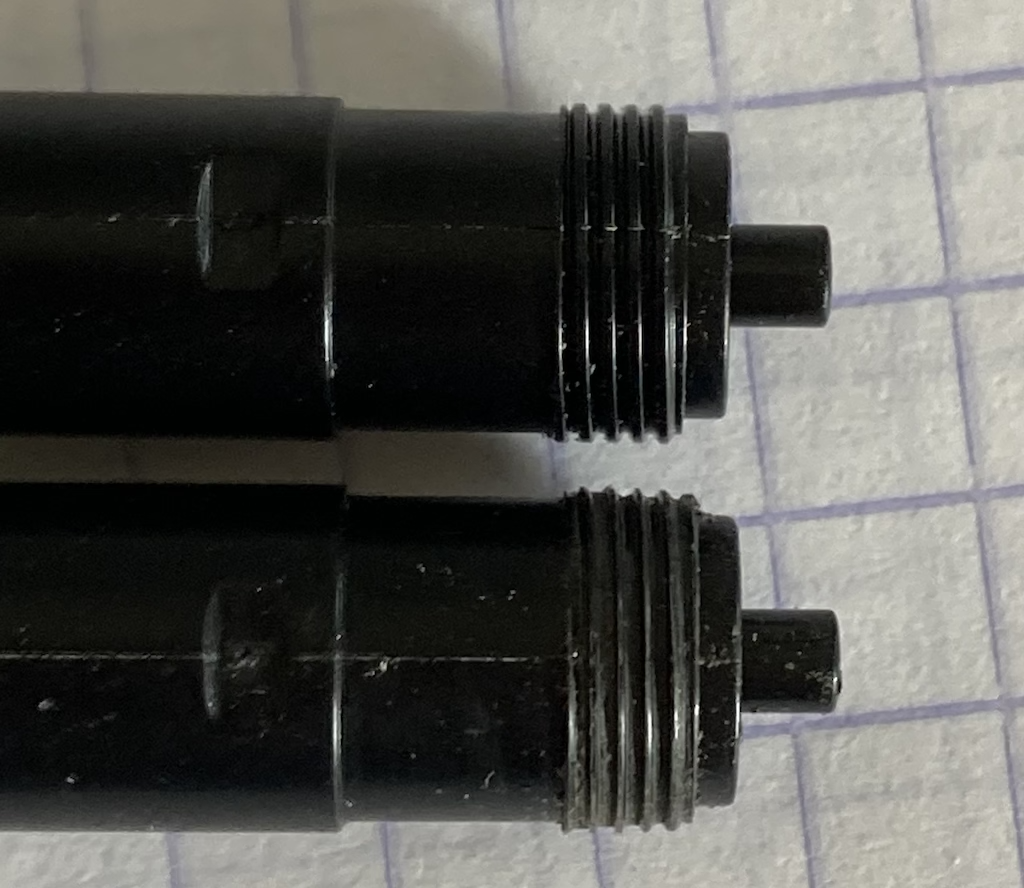
Notice in the above photo that the thread tops are sharper, for example.
After re-threading, the modified insert screwed into the ebonite test piece on the first try.
To make sure this wasn’t an accident, I repeated the whole process with 3 other insert units – all with the same result. The die trick works.
So, until FP Nibs can get a new-and-improved tap from Dabex (they’re already on the case…), this work-around will do the trick nicely.
Conclusions:
The home-made die needs some cleaning up – the chip-clearing grooves need to be bigger, and the taper increased, but the concept is working well.
Despite the small annoyance of the tap not working, the response time and communication from FP Nibs has been phenomenal. I’m certainly a happy customer. And besides, the customisation work they did on the nib that was part of my order was great. Once the pen is in the hands of its new owner, I’ll put some photos here to show the final results.
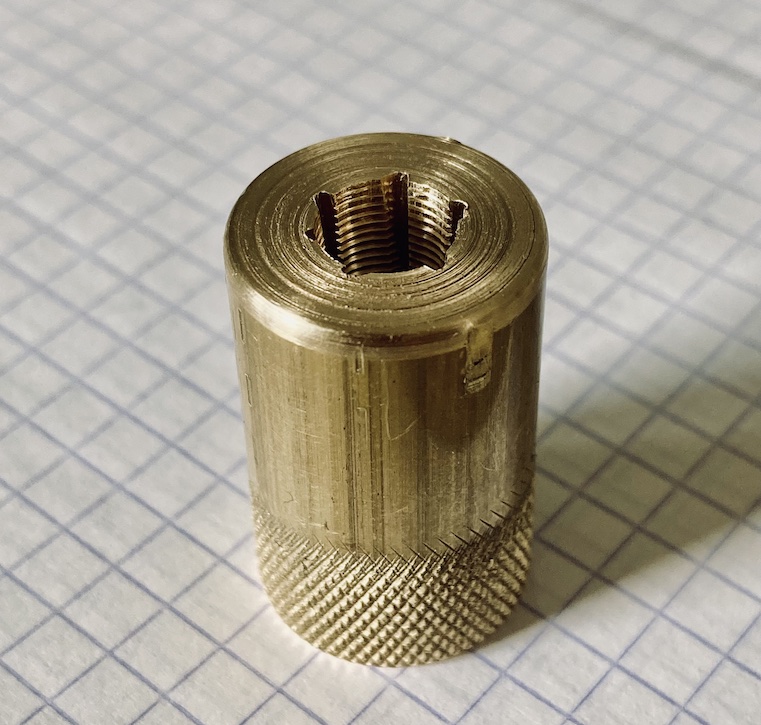
IMPORTANT UPDATE!
fpnibs.com now has the new-and-improved taps in stock. I’ve already ordered, received, and used one and it works flawlessly in an ebonite section.
One Reply to “Cutting threads for a Bock 250 insert”
Comments are closed.